As expert designers and builders of ecological systems, we have made our efforts in the study of systems for the abatement and purification of fumes from fine dust, PM 10, PM 2,5, and the simultaneous elimination of chemical compounds, produced by: civil and industrial heating systems, incinerators and waste-to-energy plants, industrial plants such as foundries, forges, blast furnaces etc. etc. that use solid, liquid and gaseous fuels.
Heating systems, waste treatment plants, industrial plants and craft activities are major producers of air pollutants, the pollutants emitted by these plants are the most varied and depend on: the type of fuel, the state of maintenance of the plant, from the processing performed.
NOTES ON THE CLASSIFICATION OF AIR POLLUTANTS
Given the great variety of substances present in the atmosphere, numerous methods of classification of air pollutants have been proposed: firstly it can be classified according to the chemical composition, for which we mainly speak of compounds that contain sulfur, compounds that contain nitrogen, which contain carbon and halogen compounds. Secondly, it can be classified according to the physical state: gaseous, liquid or solid; finally it can be divided according to the degree of reactivity in the atmosphere, in primary or secondary substances.
The primary pollutants can be gaseous or particulate type and are grouped into:
- SULFUR COMPOUNDS – The main compounds containing sulfur in the atmosphere are: sulfur dioxide (SO2), carbonyl sulfide (COS), carbon sulphide (CS2), hydrogen sulfide (H2S), dimethyl sulfate (CH3)2SO4.
- NITROGEN COMPOUNDS – The main nitrogen-containing compounds are: N2O, NO, NO2, NH3, HNO3, HONO, N2O5 and the salts of NO3, NO2, NH4. On the other hand, monoxide and nitrogen dioxide (NO and NO2) are considered pollutants.
- CARBON COMPOUNDS – In this category the main inorganic compounds are carbon monoxide (CO) and dioxide or carbon dioxide (CO2). This category includes a large number of compounds cataloged in large classes of which the main ones are: hydrocarbons (subdivided in turn into alkanes such as methane, alkenes such as ethene, alkynes such as acetylene), aromatics such as benzene, aldehydes such as formaldehyde, ketones such as acetones.
- IPA – Polycyclic aromatic hydrocarbons – A wide range of substances produced by the combustion of wood, naphtha and gas oil, the most important and unique standard is Benzo (a) Pirene, considered a strong carcinogen.
- HALOGENATED COMPOUNDS – Hydrochloric acid HCl, HF hydrofluoric acid, HBr hydrobromic acid, HCFC alkyl halides.
- RADICALS – The radicals of greatest interest, as they react with most of the organic and inorganic compounds, are the hydroxyl radical (OH) and hydroperoxide (HO2) during the day and the nitrate radical (NO3) at night.
While the PARTICULATE is classified according to the particle diameter; those with a diameter greater than 2.5 µm are considered to be coarse and those with a diameter of less than 2.5 µm are fine. Particles with a diameter smaller than 10 µm (PM10) are also distinguished as inhalable.
The main secondary pollutants of the gaseous type are:
- NO2 nitrogen dioxide formed from primary NO;
- O3 Ozone formed photochemically.
The secondary particulate may derive from chemical and physical-chemical reactions involving both primary and secondary gaseous pollutants. The best known are:
- the transformation of sulfur dioxide SO2 into sulphates SO4;
- the transformation of NO2 nitrogen dioxide into NO3 nitrates;
- the transformation of organic compounds into organic particles.
Further information about the status of air quality can be downloaded from the European Environment Agency website at the link: Air quality in Europe – 2019 report [EN].
MAIN PROBLEMS OF INDUSTRIAL SYSTEM FOR ABATEMENT AND PURIFICATION OF FUMES
The installations taken into consideration, when fed with fossil fuels, produce: water vapor, carbon dioxide (CO2), particulate like PM10 and lower, hydrocarbons (HC), nitrogen oxides (NOx) and sulfur dioxide (SO2), solvents, acid mists, metals, dust and more.
The main treatments to be carried out by the fumes coming out of these production processes concern: dedusting, deacidification and denitrification.
PROPOSED SYSTEM FOR ABATEMENT AND PURIFICATION OF FUMES
The devices designed for the abatement and purification of fumes meet the following criteria: versatility and wide range of use, reliability and durability, very low maintenance.
The equipment, highlighted in our WIEP-12445 block diagram, is mainly composed of a mist-type blast chiller with the aim of transferring the ashes and chemical compounds present in the fumes into the liquid mass, to then recover the transferred heat, purify it, neutralize it and filter it, before returning it to circulation.
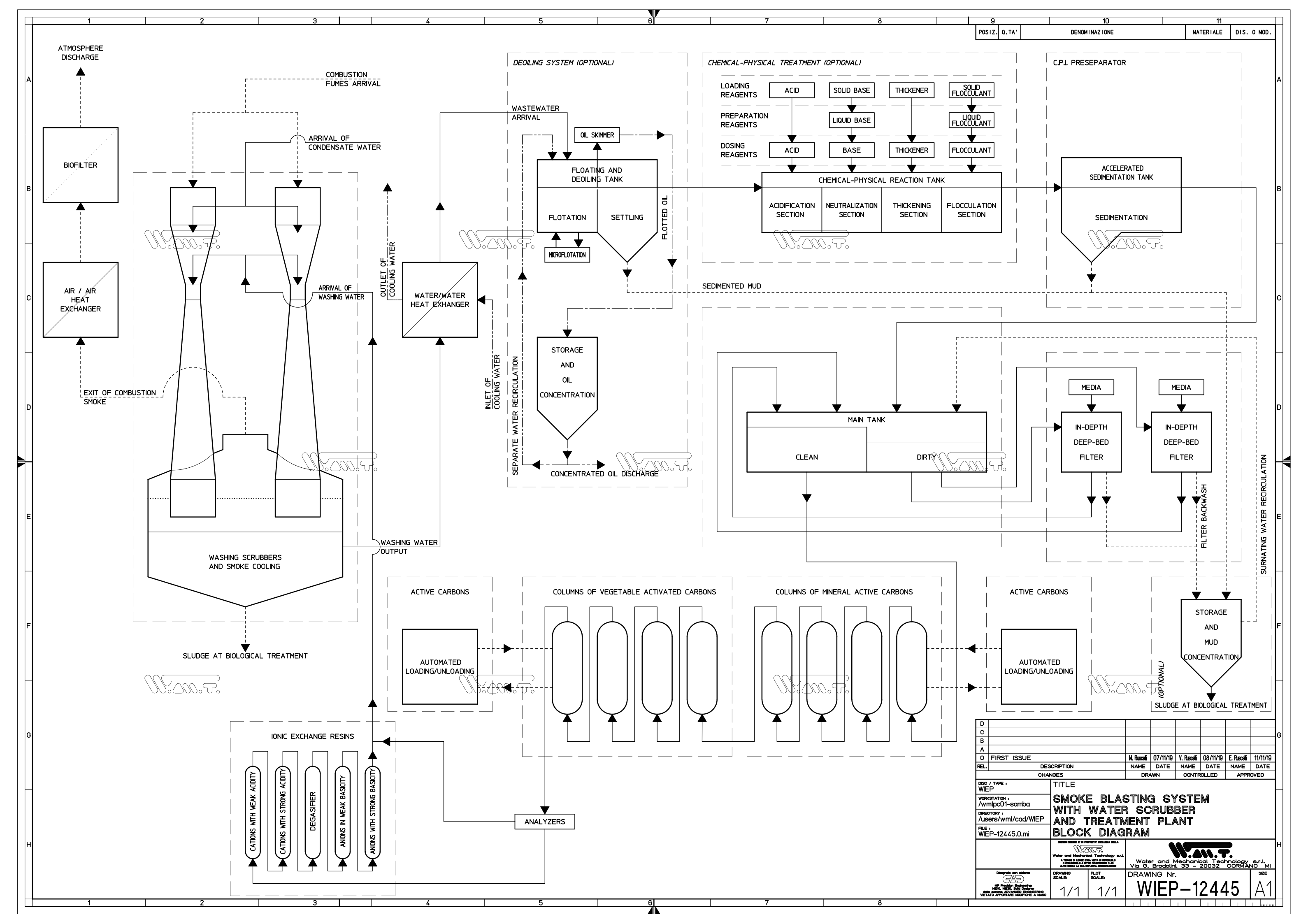
The fumes coming from the production process or from the discharge chimney are conveyed to the purifier and introduced, by means of one or more venturi tubes, into the washing chamber. In this path they come into contact with a jet of water sprayed through the motor nozzle of the venturi tube. Due to the enormous surface of contact between fumes and liquid, given by the enormous number of tiny particles of water created by the special nebulizer nozzle, we obtain – by means of the difference in surface tension between smoke and fog – a strong absorption of liquid particles by solid particles. The solid particles weighed down by the absorption of the liquid, separate from the fluid stream and precipitate in the collection tank to then be sent for treatment.
The fumes so purified, but with a rich percentage of humidity, pass through a droplet separator and a condenser in order to recirculate all the liquid used to wash the fumes and avoid fumes coming out of the exhaust expulsion into the atmosphere.
Additional outlets such as heat recuperators and other mechanical or biological filters can be installed on the exhaust fumes duct.
The washing liquid comes in the order:
- COOLED, recovering the heat removed from the fumes and used for heating or hot water generation;
- DEOILED, for the separation from the washing liquid of any oils or condensed hydrocarbons;
- THEREFORE IT CONTINUES A PHYSICAL/CHEMICAL TREATMENT PROCESS, through: acidification, neutralization, flocculation and precipitation, the chemical compounds accumulated in the liquid during the washing phase are removed;
- PRE-SEPARATE, through a device designed to increase the separation of the solid substances present in the washing liquid;
- FILTERED, through a deep bed clarifying filter, with submicron filtration degree, self-cleaning with regeneration of the filter medium by total translation in an annexed hydrocyclonic scrubber;
- FINALLY SUBJECTS A FINAL TREATMENT through passage in columns of activated carbon and/or ion exchange resins: to allow the elimination of residues of organic and inorganic micro-pollutants and restore the correct chemical parameters of the washing fluid.
- The oil, the liquids containing the separated pollutants, and the sludge coming from the various separation processes are thickened through various systems for subsequent disposal.
For any information and configuration of the system according to your specific needs, please contact our technical department.